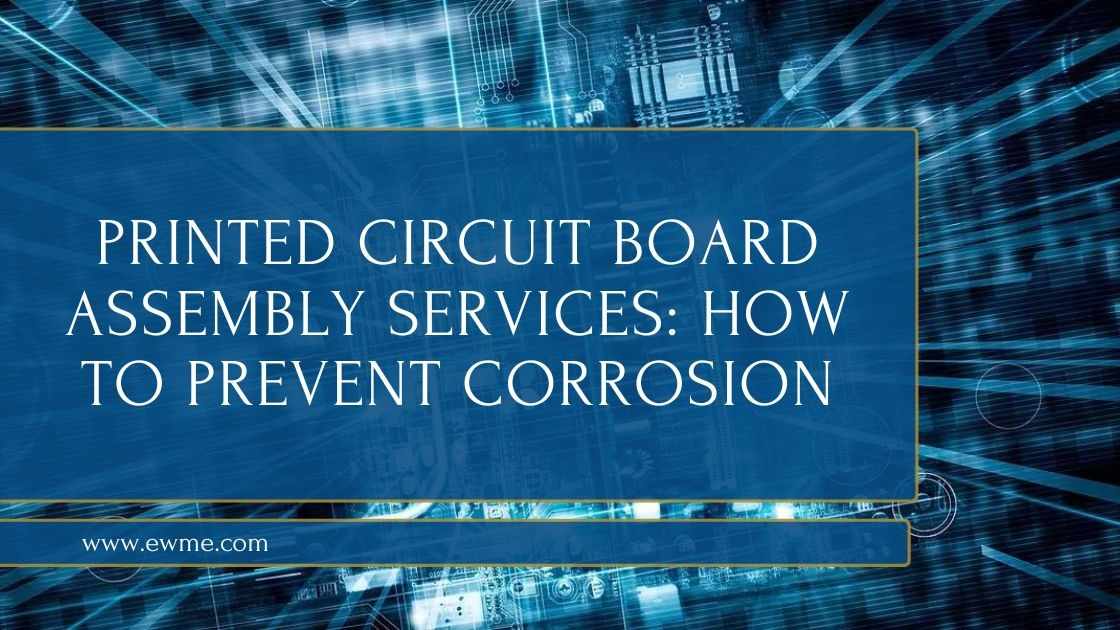
With the advent of a data-driven economy, we all depend on complex circuit boards for everything. Learning how to build and provide PCB Assembly Services is the central task of any technician in this field. However, the management of the systems is of even more importance. Today's blog focuses on one of the principal problems on a circuit board assembly service - corrosion.
4 Tips to Maintain Corrosion-Free PCB
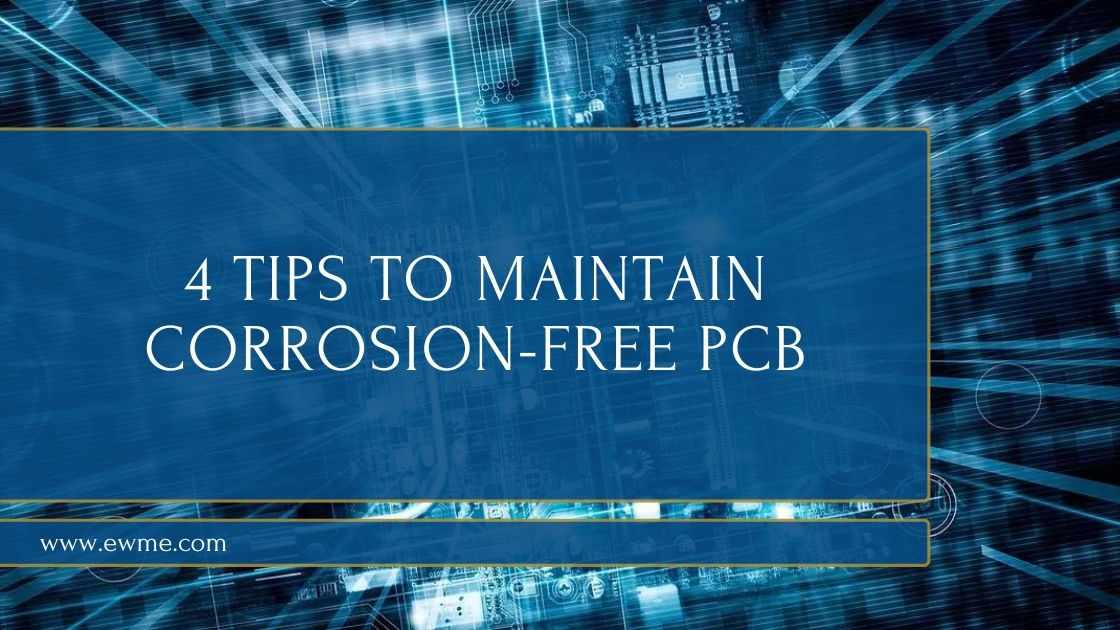
Cleanliness and Contamination Control
Indeed, one of the most overlooked causes of a dirty and corroded circuit board is the accumulation of dust and pollutants on its surface.
We all know how fragile the tiny parts on a Build To Print Manufacturing system can be; and grime can get right into the greeks and crewises of these parts allowing for moisture to build up - essentially causing a deep level damage that is impossible to cure.
Environmental Protection Measures
Ideally, the printed circuit board should never be left out in the open where it can directly come in contact with humidity and air molecules. There are several great but affordable ways of storing PCB where it is safe.
These can include:
Storing PCBs in a dry and cool place, away from direct sunlight
Covering them with a shade made of corrosion resistant materials
Use anti-static bags and desiccant packets, for protection
Never bringing the unit close to extreme temperature or great temperature fluctuations
Material Selection and Design Considerations
During the NPI electronics manufacturing process, it is possible to keep material selection and design under strict control. In fact, this is a vital necessity if we want to protect the production quality of a PCB.
There are several steps during designing, prototyping and actual circuit boards set up where strict ethical standards and regulations can be imposed so that we stay away from low quality materials that can easily get corroded.
Conformal Coating Application
This is all about applying a clear, protective layer on top of the board components. Its job is to protect the board from moisture and dust.
The application process of this coating substance is easy and quick. The layer is applied using a variety of methods, like spraying or dipping, and then it's cured in an oven to make it all hard and durable.
The better quality the conformal coating, the longer a PCB board is likely to last in environments that are corrosive to its body.
Last Thoughts
A proper management of the corrosion is also helpful when administering the proper solution. We should understand that PCB getting corroded can have several reasons - being exposed to moisture, humidity, or water; being set up against leaking, harmful chemicals etc. These things can happen due to poor storage, humid environments, or physical damage. A bad PCB is infectious to all other components of the system, so treating it is crucial.
Write a comment ...