There is perhaps any industry in today’s date that does not use a printed circuit board assembly. However, one of the pioneering areas of research for this niche is how to maximize the use of PCB in defense electronics manufacturing without affecting the quality of production in any way. Several recent tools and vehicles produced by the military have printed circuit boards inside them. Here is a guide to the four main types of PCB that are found in defense design.
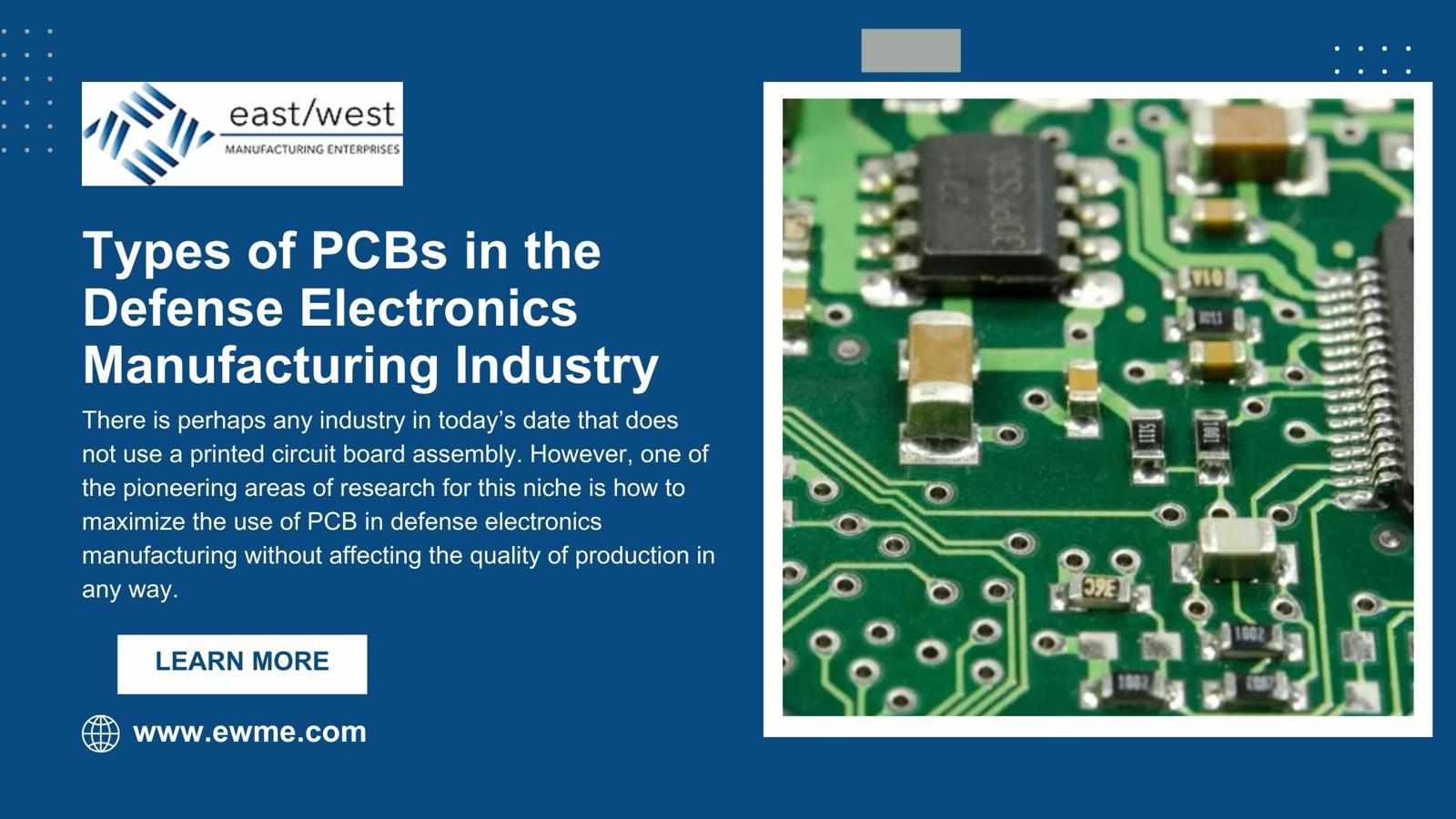
4 Types of PCB Assembly Used in Defense Design & Manufacturing
Rigid Printed Circuit Boards
Rigid PCBs are the most common type of circuit board – they’re stiff and don’t bend.
These items are great because they have amazing surface durability and can withstand very high blunt force. They’re great also because they’re reliable and easy to manufacture on a budget.
However, RPCBs can be bulky and heavy, making them less ideal for wearable tech or inconspicuous devices. But hey, they’re perfect for bigger gadgets like military computers!
Flexible Printed Circuit Boards
These can bend and twist without breaking! They’re super thin and lightweight, making them perfect for wearable tech, medical devices etc.
Not only are they physically flexible but these designs can be highly modifiable according to the situation. They can break easily but this breakage is not that much caused by bending or falling.
The downside? They can be a bit hefty on the purse. They also wear and tear more quickly than the rigid ones.
Rigid-Flex Printed Circuit Boards
Ever met someone who can be both assertive and friendly at the same time? That’s rigid-flex for you! They have flexible sections that connect rigid areas, making them perfect aerospace and defense technology.
They’re pricier than rigid PCBs and can take a little more time to be made. These circuits can be attached between two drastically different types of devices which is why they are a common pick for any experimental device in its early stages.
High-Density Interconnect (HDI)
An integration system needs as much versatility as it can get. Maximizing all three areas of durability, spread and flexibility, HDIs can cram 100s of different connections in millimeters of space and drive high-level data between them.
They use tiny vias and tight trace spacing to create super-dense circuits, making them perfect for apps that need serious processing power, like smartphones, laptops, and medical devices.
The military needs HDI technology to pack advanced computing power and sensor capabilities into smaller, lighter, and ruggedized devices.
Last Thoughts
If any design fails the PCB functional testing, there is a chance that this is because of using the wrong kind of PCB board. Functional testing is just a way to make sure a circuit board works as it should but in the military, they take it to the next level by simulating real-world scenarios and pushing it to its limits to ensure it performs flawlessly, even in tough conditions. They want to know it’ll work right when they need it most!
Write a comment ...