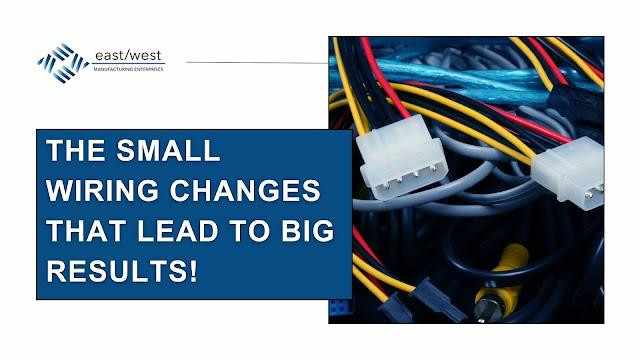
When your wire harness falls apart mid-project, you're not just wasting time; you're hemorrhaging money. Every minute of downtime costs real dollars, and no engineer wants that nightmare. This guide will teach you exactly how to put an end to wire harness assembly problems dead in their tracks.
Challenges of Manufacturing
Wire harness assembly is far from just connecting some wires. It's precision dancing that one wrong move can blow your whole operation to smithereens. What professional technicians know is the subtlety of these details most people miss.
Common Mistakes to Avoid
Several factors can cause wiring problems. Temperature fluctuations, mechanical strain, and inappropriate material choices can transform simple projects into nightmares. Cable and Wire Harness Assembly Austin experts witness this every day.
Material Selection Matters More
Not all wires are created equal. Choosing the wrong wire gauge or insulation type leads to catastrophic failures. High-quality materials resist wear, temperature extremes, and mechanical strain. Think of your wire harness like a professional athlete—it needs top-tier equipment to perform consistently.
Precision Matters in Every Connection
Sloppy connections ensure failure. Crimp quality is crucial. A loose connection leads to resistance and heat buildup, which can cause the system to fail completely. Professional-grade crimping tools aren't a want; they are a must-have.
Technical Preparation Prevents Performance Problems
Quality planning will tell the difference between the hits and total misses of a project with Wire Harness Assembly Austin. Robust documentation, extensive test procedures, and quality assurance result in predictable, safe results.
Testing is recommended for survival. Electrical continuity checks, insulation resistance tests, and mechanical stress tests could identify potential weaknesses and even prevent catastrophic failure.
Environmental Considerations Kill Unprepared Projects
Temperature, humidity, and mechanical vibration destroy poorly designed wire harnesses. Your assembly must withstand extreme conditions without compromising performance. Military-grade standards aren't just for defense contractors—they're a blueprint for exceptional engineering.
Heat destroys wire harnesses faster than anything else. Proper routing, heat-resistant materials, and strategic spacing prevent thermal degradation. Smart engineers think three steps ahead.
Advanced Strategies for Aftermarket Services
Retrofitting existing wire harnesses requires surgical precision. Understanding original design constraints while introducing modern improvements demands expert-level skills. Successful technicians blend respect for original engineering with innovative problem-solving.
Accurate records turn Aftermarket Services Austin from guessing games into predictable success. You have detailed schematics, material specifications, and performance logs to guide you through complex retrofitting challenges.
Conclusion
Wire harness assembly isn't rocket science, it's careful, methodical engineering. By understanding material properties, testing rigorously, and planning meticulously, you can convert potential failures into consistent victories.
Professional engineers do not hope for success in engineering. Your wire harness is more than just a component; it's the nervous system of your entire project.
Write a comment ...